A Swiss company says it’s come up with a process that could help prevent a real barrier for some consumers to buying an electric vehicle—fear that it may suddenly go up in flames. That’s what happened to a Tesla EV in April, 2019 in Shanghai while it sat in a parking garage.
“That fire occurs because water gets into the cell and this reaction that happens is very volatile, sometimes can explode, catch on fire,” said Thomas Parker, North American sales manager for battery leak detection technology company, Inficon.
The company, with North American headquarters in Syracuse, N.Y., announced today it has developed a system called the ELT3000, that can detect battery leaks 1,000 times smaller than currently possible using other methods. Indeed, Inficon says, with its system, for the first time, battery cells can be tested after they’re filled with electrolyte.
The result could be flagging lithium-ion batteries at risk of absorbing dangerous moisture before they’re installed in vehicles.
Developed at Inficon’s Cologne, Germany research facilities, the ELT3000 uses mass spectrometer technology. As Parker explained in an interview, it’s actually a modification of a system that’s been in use for almost 20 years by manufacturers of items such as refrigerators, air conditioners and freezers.
“We have modified it significantly for the detection of electrolyte for these battery cells,” explained Parker. “The way we do this is we look for literally molecules of material coming out of the cell. So if you look at the molecular size of materials coming through a hole or defect, significantly smaller than a visual test, or air pressure decay test, the reason is it has to be so small we can be assured moisture will not ingress into the cell.”
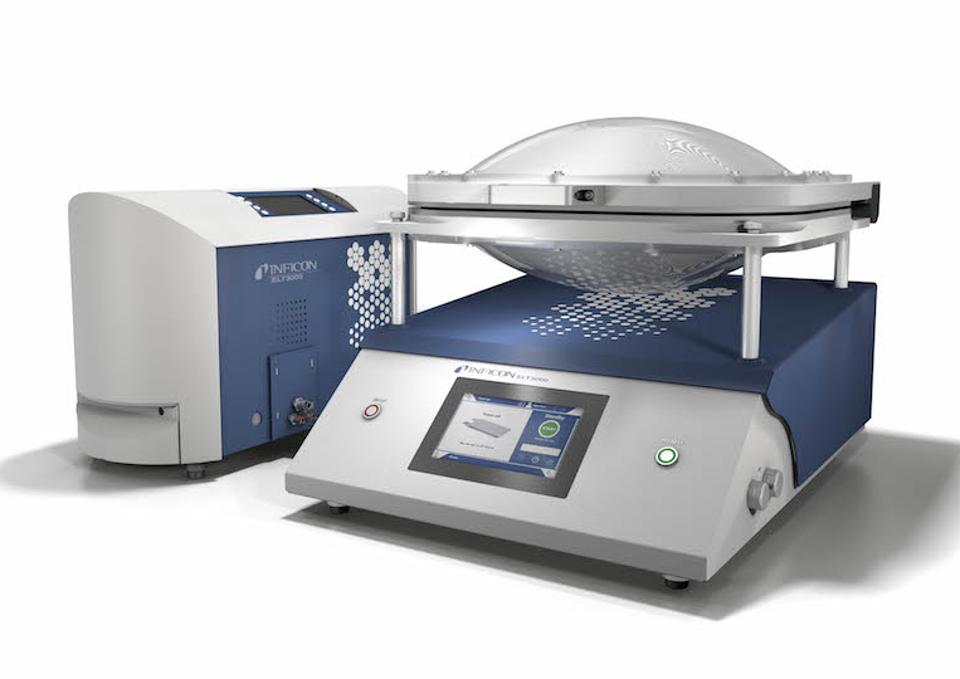
Inficon first discussed its innovation over the summer in an SAE international paper entitled, “Methods for Leak Testing Lithium-Ion Batteries to Assure Quality with Proposed Rejection Limit Standards.”
The company actually discovered the need for tighter battery leak testing while working with several companies in Asia that suspected current testing methods were missing some flaws.
“Our customers would say, we’re pretty sure this thing is leak tight but when we put that electrolyte in and we cover up that hole, we’re not so sure and we’d like to have a final electrolyte test to test the integrity of the hole container once it’s been built with electrolytes,” said Parker. “That need from customers spurred our development for this product.”
While spontaneous combustion represents one mode of failure in an EV’s battery, other, less dire results can occur when moisture finds its way into the cell according to Parker. Those results would appear to the consumer as a loss of driving range or an extended time to recharge the cells.
He says Inficon is currently working “globally with all major electric vehicle manufacturers and cell technology providers.” The ELT3000 leak detection system would be used after the battery manufacturer fills the cell with electrolyte and before the cell is installed in the battery pack, Parker explained.
The need to ensure the integrity of batteries for battery and hybrid electric vehicles looks to become even more vital as production of such cars and trucks explodes. Parker estimates the global market for battery cells will grow from an expected $44 billion this year to “nearly $95 billion” in 2025.
But Inficon is looking beyond testing only EV batteries saying ELT3000 could also be used to detect leaks in batteries that power smart phones, computers and other consumer electronics.